Inter-University Accelerator Centre
The Pelletron accelerator laboratory at IUAC has been operational since July 1991. It has completed 29 years of successful operation. Over the years since its installation, it has been providing ion beams to more than 400 users from India and abroad. The majority of the user communities are from universities in the country. The 15 UD Pelletron with six established beamlines provides ions beams for experiments involving basic and applied research in nuclear physics, atomic physics, material science, atomic mass spectrometry, biosciences, and other allied fields (phase I). The accelerator has been operational over a wide range of energies. To pursue experiments involving higher energies, the energized particles delivered from the Pelletron are further subjected to the LINAC facility to boost up the energy. With this extended setup (or Phase II), the established experimental facilities are GPSC II (General Purpose Scattering Chamber II), Material Science II., HYRA (HYbrid Recoil mass Analyzer), and Atomic physics.
Pelletron Accelerator
The 15 UD Pelletron is a tandem electrostatic accelerator capable of accelerating ion beams of all essentially stable nuclei with energies up to 200 MeV depending on the ion species. The ion source for this machine is Multi cathode cesium sputter negative ion source. The negative ions are produced and pre-accelerated up to ~ 300keV in Ion Source. The desired ion beams are selected and also bent from the horizontal plane to the vertical plane using an Injector magnet. These ions are injected into the 15 UD pelletron for acceleration. The electrostatic accelerator is installed in vertical configuration inside a tank filled with SF6 insulating gas. The tandem accelerator has both ends at the ground with high -voltage terminal at the middle. The terminal is connected to the tank vertically through accelerating tubes. These tubes maintained a potential gradient from the tank top to the terminal as well as from the terminal to the tank bottom. Two metal pellet charging chains are used for the generation of high voltage at the terminal. This terminal can be charged to a high potential that can be varied from 4 to 15 MV. The principle involved in generating high voltage at the terminal is the Van de Graaff generator.
The acceleration is due to the electrostatic attraction between the negative ions and the high positive potential terminal. The terminal is equipped with a gas stripper differentially pumped by two turbopumps. It also has a foil stripper assembly. On reaching the terminal they pass through a stripper which removes electrons away, thereby converting them into positive ions. These ions are again accelerated to ground potential to the tank bottom. In this case, the acceleration is due to electrostatic repulsion between the high terminal potential and the resulting positive ions. Hence, the ions emerging out of the accelerator have energy gain E= V(q+1), V = terminal potential, q = charge state of the positive charge after stripping. These high-energy ions are then analyzed to the required energy with an analyzer magnet. The ions are bent into a horizontal plane by this magnet. The ions are directed to a desired experimental area with a multiport switching magnet that can deflect the ion beam into any of the six established beamlines. In addition to the DC beam (continuous beam), it can deliver a pulsed beam of 1.2ns to 2 ns width separated by 250ns to 2us could be delivered with multi harmonic buncher in the low energy section. The entire machine is computer-controlled and is operated from the control room.
Beams Delivered by Pelletron accelerator
Following Beams are majorly delivered by Pelletron accelerator to various experimentalists:
1H, 6,7Li, 9Be, 10,11B, 12,13C, 14,15N, 16,18O, 19F, 24Mg, 27Al, 28,29,30Si, 31P, 32,34S, 35,37Cl, 40Ca, 45Sc, 46,48Ti, 51V, 56Fe, 58Ni, 63Cu, 64Zn, 74Ge, 79Br, 107,109Ag, 120Sn, 127I,197Au and 208Pb
Operational Statistics
The operational summary of the accelerator from
April 2019 to March 2020 is mentioned below.
- Total No. of Chain Hours
5161 Hours
- Total Beam utilization
3179 Hours
- Machine breakdown
0308 Hours
- Accelerator Conditioning
0806 Hours
- Beam Change Time
0005 Hours
- Tank opening maintenance
2978 Hours
- Tank opening maintenance
2978 Hours
- Beam tuning time
0147 Hours
- Experimental setup time
0020 Hours
- Accelerator set up time after maintenance
0117 Hours
- Total No. of Experimental Shifts
398 Shifts
- No of Shifts of Pulsed beam
235 Shifts
- No. of Shifts with DC bram
163 Shifts
Chain Hours Utilization
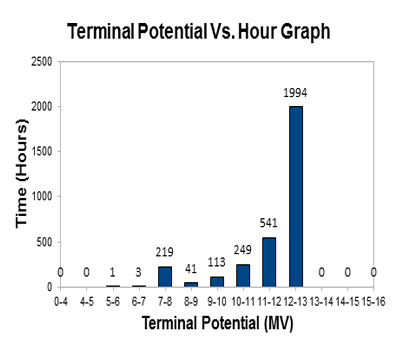

DEVELOPMENTS
Over the years, the applications of electrostatic accelerators have broadened into a wide variety of fields. Thereby, these demand improvements in the performance of the accelerator such as beam quality, beam intensity, beam transmission, etc. There have been considerable improvements to upgrade various features of the 15 UD Pelletron accelerator machine. Some important features among them are listed below.
ION SOURCE
The ion source in the injector system was equipped with NEC made single sample SNICS source (Source of Negative Ion by Cesium Sputtering), a sputter negative ion source. In the year 2002, MC-SNICS ion source with a maximum capacity of 40 samples at a time, replaced the old source. The main purpose for this replacement was due to the ongoing AMS program which required higher output source with high precision in changing the sample position. The cathode wheel movement of the source installed was unidirectional. The bidirectional movements of the cathode wheel and its remote control to change the cathode position had been indigenously developed. It reduces the time required to change the samples and also improves the life of the source components. We have encountered many operational limitations with this source. The source needs servicing frequently due to the constant high flow of cesium which leads to floating cathode contact, shorting of the cesium focus lens, einzel lens, and the general-purpose acceleration tubes. In March 2012, an upgraded version of the MC-SNICS source replaced the old one to avoid all these operational limitations. The internal assembly of the old source is modified and cesium focus is no longer in use. The Cesium reservoir and cesium oven heater design have been modified. The new source is equipped with a spherical ionizer, immersion lens, cesium flow diffuser. This replacement results in a not only improvement in beam current with much better emittance but also in operations and maintenance. The modified MC-SNICS ion source has many advanced features over the old source. Few of them are like the spherical ionizer focuses the cesium beam at the cathode target sharply so that 90 -95% of the target material can be used to produce an ion beam. Cesium diffuser diverts cesium only to the surface of the spherical ionizer, which in turn reduces the number of the maintenances which were caused by cesium. Vacuum insulated cesium feed line allows normal operation of source with lower oven temperature, 90 deg C. Hence, the migration of cesium vapor to the extractor lens and GP tubes does not occur.
ACCELERATOR
- Resistor based voltage grading system: The accelerator had corona based voltage grading system to define the potential both along with the column support posts and the accelerating tubes. As the pelletron facility provides beams to the needs of an academic community with wide-ranging research interests, the terminal potential and ion beam species had to be varied over a large spectrum. In the corona-based system, large changes of terminal potential could be accomplished by the use of shorting rods and changes of insulating gas pressure only. Resistors of 3 Gega ohm, 40 kV, + 2% values were used to install a resistor-based voltage grading system. As a result of this upgradation voltage stability of the accelerator has improved and no shorting rods are used now for generating variations in terminal voltages. After a few years of operation, resistances were falling off the column support posts and a new rigid mounting system utilizing the corona mounting brackets attached to the column support posts has been implemented. In the column support posts, the pair of 3 Gega ohm resistances have been connected by a flexible braid, preventing resistance breakage due to excessive vibration which was earlier happening
- Welwyn Resistors ( 3 GW, 40 kV , + 2 %)
- Better Voltage Stability ( App . 2 kV IN 15 MV )
- Large terminal potential variation without shorting rods (2.93 TO 15.3)
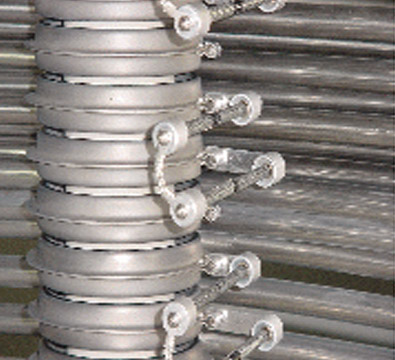
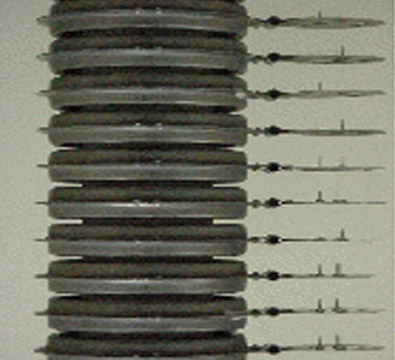
- Charging chain monitoring system by pick-up rings: Capacitive pickup rings were installed around the pelletron chains to observe uniformity of charge distribution on the pellets of the chains. Monitoring of charging chains is done with this online monitoring system and it was observed that monitoring of the chain oscillations, chain frequency, and other variations in the signal patterns help in maintaining a long-lived charging system.
- Conversion of Double Unit Structure to Single Units: The accelerator structure has its columns arranged in terms of double units with each double unit consisting of six 11 electrode tubes and one shorter 8 electrode tube. In the 15 UD machines on each side, there are 7 such double units and one singlet consisting of 3 full-lengths (11 gap tubes) and one 4 gap tube. During shorting rods operation for terminal voltage reduction one could short only a double unit at a time. In case of any problems, one could pinpoint only the doublet structure. Further during unit-wise conditioning to bring the terminal voltage up one had to condition the machine by 2 units at a time. The machine units configuration has been reorganized by connecting the center point of each 8 gap tube to a corresponding casting plate through a GI wire. The system has functioned well and extensive unit-wise conditioning is done with this technique.
- Installation of Faraday Cup -031:A faraday cup was installed at the exit of the accelerator (outside the tank) to monitor beam current. This helps in improvements of transmission of the beam current and also easier for tuning the beam.
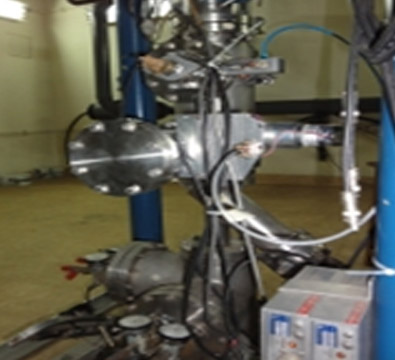
Beam Pulsing System:
The Beam Pulsing system was upgraded by installing a new multi-harmonic buncher. The beam pulsing system has the following features:
- Multi Harmonic Buncher operates with a fundamental frequency of 12.125 MHz and it can use up to 3 harmonics.
- Spiral cavity was installed to avoid phase drift due to variation in flight path of the beam through the accelerator.
- Efficiency of the bunching is 50%
- The time resolution achieved for various beams is 1.2 ns to 2 ns.
- Chopper and TWD may also be used to give repetition rates between 250ns to 2 μs. The Multi-Harmonic Single Gap Buncher, operating at the bunching frequency of 12.125 Mhz and its harmonics, can provide a pulsed beam of more than 50% bunching efficiency. The typical time resolution achieved is between 1 to2 ns.
Stripper:
- The Recirculating gas stripper system: A new recirculating Turbo Molecular pump-based pumping system has been designed and installed in the high voltage terminal of 15 UD Pelletron. The system has been installed and is being used for regular accelerator operation. The system has helped improvements in the vacuum inside the accelerator during gas stripper runs and excellent improvements in beam transmissions. Two turbo molecular pumps have been installed in place of sublimation pumps and their backing ports have been connected to the inlet line of stripper gas. The stripper gas emerges from the canal into a large volume pumped by two turbopumps and the gas is recalculating to the stripper canal. Though the differential pumping reduces the gas escape to the accelerator tubes any losses of gas are compensated for by the introduction of fresh gas. The recirculating gas is passed through a hydrocarbon filter to prevent any hydrocarbons from mixing with the stripper gas. There is a significant improvement in overall beam transmissions. The machine vacuum during gas stripper operation has improved and in brief, this configuration has made this machine a versatile machine. It has made it possible to deliver beams of very low energies also which was not possible with the previous configuration of gas stripper.
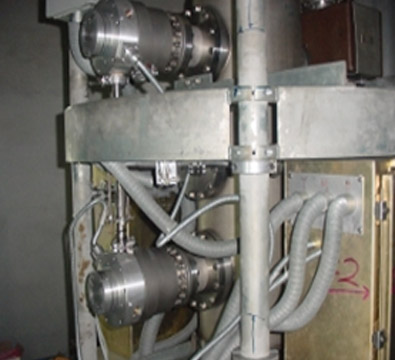
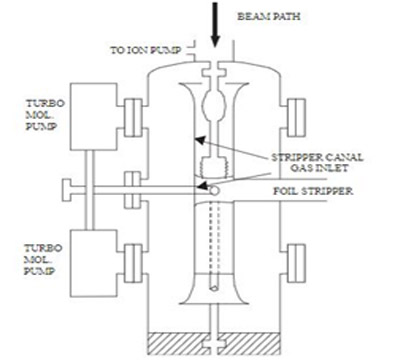
- Development of foil stripper position read back system: An entirely new system was designed, fabricated, tested, and installed. This system can count precisely, the position of the foil stripper from 1 to 200 in increment mode and 200 to 1 in decrement mode. The new system has an electronic UP/DN counter instead of a mechanical counter. This avoids the problem of incorrect reading due to slippage and counts from 1 to 200 and resets to initial count 1 for the next count after 200. It also uses a much improved 8 bit DAC that gives accurate and linear output and this system has a local display of stripper position read back.
- Foil strippers: Home-made foil by Evaporation Condensation (E-C) technique of 4 ug/sq.cm were used but recently we have started using laser-plasma ablated (LPA) foils and these foils have improved the life of stripper foils. The stripper foils had to be replaced every six months. The E-C foils have a very short lifetime when irradiated with heavier beams like I, Ag, Au, etc. LPA foils are known to exhibit a longer life against radiation damage because of its structure is composed of randomly oriented nano crystals. Two foils stripper assemblies, one each before and after analyzing magnet, have been added for producing higher charge state beam for LINAC and for those experiments requiring higher charge state accelerated ion beams. These foil stripper assemblies have a capacity of loading 50 foils of 5/8 inch diameter. Two controllers were developed and installed to control the operation of newly installed foil stripper assemblies. A position read back system was also designed by using a 3 digit BCD UP/DOWN counter with a DAC and these are being used for position read back of all the foil stripper assemblies in the system
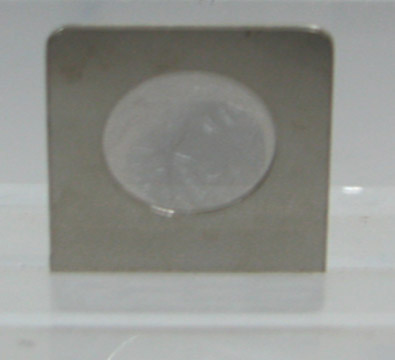
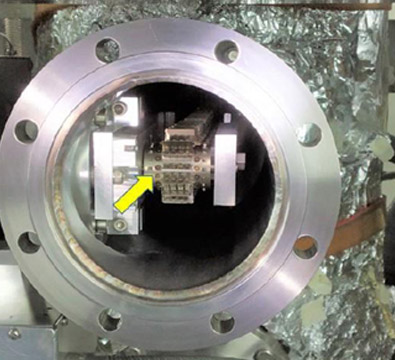
- Stripping of Molecular Beams (e.g. MgO ):
- *Gas + Foil stripper combination used for increased beam current
- *Stripping of negative ions by foil lead to high charge states.
- *Coulomb explosion & high divergence of atoms. Beam current reduces.
- *Gas stripper leads to low charge states.
- *Less coulomb repulsion.Reduced divergence.
- *Subsequently, atomic beam further stripped in foil stripper. High charge state.
- *Desired energy E = (q+x)V , Where x= Molecular fraction obtained.
- Example:Input current: 200nA.
- 24MgO6+ : Analyzed current: 12nA= 2pnA.
- For terminal potential of 12 MV & stripper gas pressure ~ 200 micron.
- Improvement of 50% from foil stripper alone.
Chiller:
- A new SF6 chiller replaced the chiller which was being used in side accelerator tank to regulate the temperature of SF6 gas inside tank at around 25 deg C. This new chiller is installed outside the tank. This is done to avoid any kind of accident which may occur during the operation of accelerator. It is of shell and tube type. Chilled water is circulated in the tube which cools SF6 gas present in the shell. The designed heat load for this chiller is 16,500 kcal/hr. Fabrication of this chiller is done by a local vendor (Air Fridge).
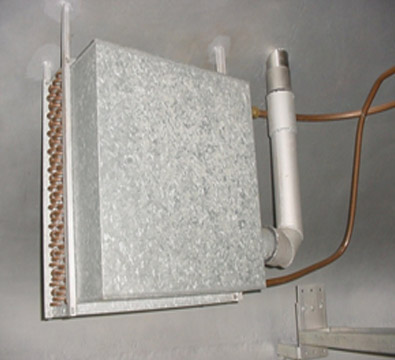
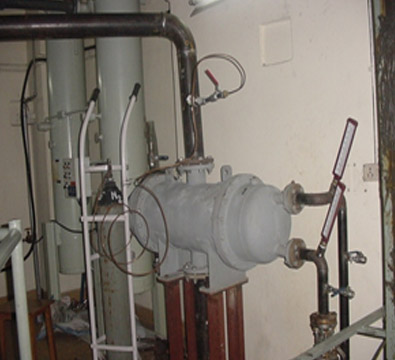
Group members and contact address
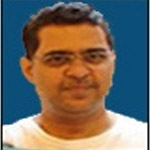
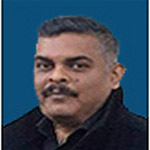
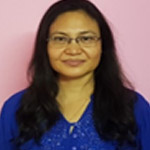
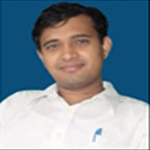
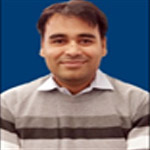
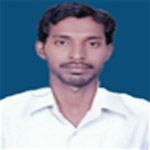

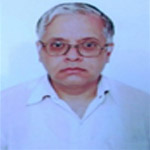
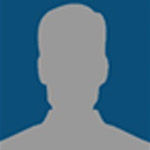
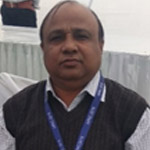
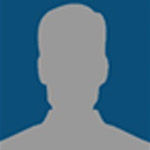
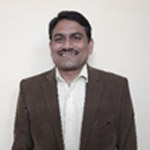
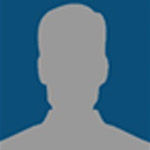
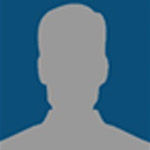
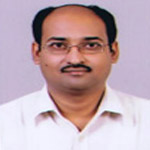
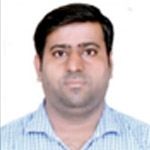
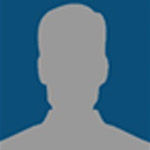